Loại hao tổn thứ hai là các công việc chuẩn bị trước khi sản xuất. Để chuẩn bị cho sản xuất, những người thợ cơ khí, bảo dưỡng thường tốn rất nhiều thời gian cho công việc chuẩn bị máy
Cài đặt và hiệu chỉnh thiết bị
Loại hao tổn thứ hai là các công việc chuẩn bị trước khi sản xuất. Để chuẩn bị cho sản xuất, những người thợ cơ khí, bảo dưỡng thường tốn rất nhiều thời gian cho công việc chuẩn bị máy. Có một hệ thống giúp công việc chuẩn bị đạt hiệu quả đó là SMED (tính thời gian chết - Single Minute Exchange of Die) được phát triển ở Nhật Bản do Shigeo Shingo sáng tạo ra. Có 2 yếu tố cần loại mà SMED cho là tiêu điểm: một là các công việc trước chuẩn bị như thời gian chuẩn bị cho các yếu tố bên trong thiết bị (thời gian khi thiết bị ngừng hoạt động) và thời gian chuẩn bị các yếu tố bên ngoài (thời gian khi thiết bị đang hoạt động) quá nhiều. Yếu tố còn lại là các sự điều chỉnh thông số kỹ thuật của máy móc thiết bị... để hoàn thành công việc chuẩn bị trước khi sản xuất. Nếu áp dụng kỹ thuật SMED có thể giúp giảm thời gian chuẩn bị, khi đó lượng thời gian giảm được sẽ chuyển sang thời gian hoạt động của thiết bị. Do đó, việc áp dụng kỹ thuật SMED sẽ làm gia tăng đáng kể hệ số sẵn sàng của thiết bị.
Thiết bị chạy không tải và bị gián đoạn khi đang vận hành
Thiết bị chạy không tải và bị gián đoạn là 2 nguyên nhân lớn nhất gây ra thời gian chết của máy. Thiết bị bị gián đoạn khi đang vận hành xảy ra khi một bộ phận của hệ thống sản xuất gặp sự cố đột ngột, cài đặt thiết bị không hợp lý, hay có thể là do nguyên vật liệu không bình thường. Nói cách khác sự cố máy dừng là do công tác vận hành kém hiệu quả. Cụ thể là do việc phải chờ đợi nguyên vật liệu và các thông tin liên quan tới công việc sản xuất; thông tin công việc không được hoàn thành, không rõ ràng, hoặc bị bõ lỡ; chờ đợi sự chấp thuận của khách hàng; và nguyên vật liệu không đầy đủ. Các sự cố làm gián đoạn quá trình sản xuất thường ít được quan tâm bởi các nhà sản xuất, và điều đó giải thích tại sao nó luôn xảy ra trong suốt một thời gian dài và vẫn còn tiếp diễn trong các phân xưởng. Để đưa quá trình sản xuất trở lại bình thường thì cần phải thay đổi nguyên vật liệu, thiết lập lại các bộ phận của máy, giảm tốc độ vận hành của thiết bị… Các loại gián đoạn này có thể được khắc phục dễ dàng nhưng cũng gây ảnh hưởng không nhỏ, thậm chí là làm giảm hiệu suất hoạt động của thiết bị. Sự cố này rất khó quản lý và xác định số lượng, do vậy các tác động của nó đến thiết bị thường không thể thấy được. Vì vậy, việc loại trừ những gián đoạn không đáng có này là rất cần thiết.
Duy trì trạng thái làm việc tốt nhất của thiết bị, thiết lập chương trình đào tạo hiệu quả, thực hiện các phương thức vận hành hiệu quả và đúng tiêu chuẩn là cách duy nhất để loại trừ được những nguyên nhân gây nên các gián đoạn không cần thiết.
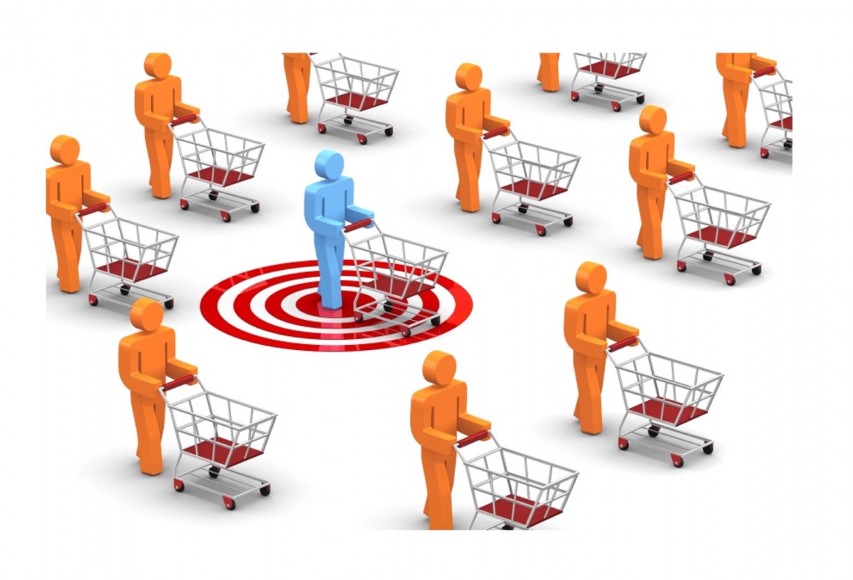
Quản Lý Quan Hệ Khách Hàng(CRM) là một phương pháp thiết thực, mạnh mẽ và hiệu quả nhất cho việc duy trì và tạo ra...
Để duy trì một thương hiệu có uy tín và lâu dài, doanh nghiệp cần phải đầu tư xây dựng thương hiệu. Thế nhưng đầu...
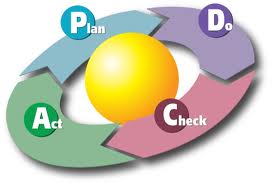
Tiếp sau chương trình áp dụng ISO 9000 trong các ngành sản xuất, từ năm 2002, Uỷ ban nhân dân thành phố Hà nội...
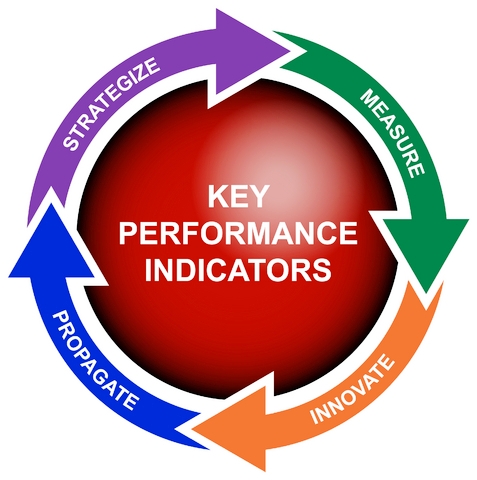
KPI là phương pháp Đo lường hiệu suất (kết quả thực hiện công việc) bằng cách thiết lập một Hệ thống chỉ số...
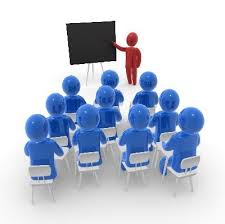
Thực hiện TPM là một quá trình học tập không ngừng. Công nhân vận hành thiết bị phải thường xuyên được huấn...